Aluminum-silicon (Al-Si) alloys are among the most widely used aluminum casting materials due to their excellent castability, lightweight nature, and good mechanical properties. The addition of silicon (typically between 5% and 20%) enhances fluidity, reduces shrinkage, and improves wear resistance, making these alloys ideal for automotive, aerospace, and industrial applications.
Aluminum-silicon (Al-Si) alloys are primarily used for casting applications (like engine blocks, pistons, and automotive parts) due to their excellent castability, good corrosion resistance, and high strength-to-weight ratio, with silicon improving fluidity and reducing shrinkage during solidification.
Composition and Key Properties
Al-Si alloys consist primarily of aluminum (Al) and silicon (Si), often with small additions of magnesium (Mg), copper (Cu), or nickel (Ni) to enhance strength and heat resistance.
Key Properties:
✔ Excellent Castability – Silicon improves molten metal flow, allowing for complex shapes.
✔ Low Thermal Expansion – Reduces warping and cracking during cooling.
✔ Good Corrosion Resistance – Performs well in harsh environments.
✔ High Strength-to-Weight Ratio – Lighter than steel but strong enough for structural parts.
✔ Wear Resistance – Silicon particles increase hardness and durability.
Common Al-Si Alloys and Their Uses
Alloy | Silicon Content | Key Features | Applications |
---|---|---|---|
A356 (AlSi7Mg) | 6.5–7.5% | Heat-treatable, good strength | Automotive wheels, engine blocks |
A380 (AlSi8Cu3Fe) | 7.5–9.5% | High pressure die casting | Transmission housings, pump bodies |
4047 (AlSi12) | 11–13% | Excellent brazing & welding | Heat exchangers, welding wire |
AlSi18 (Eutectic) | ~18% | Low melting point, high wear resistance | Pistons, bearings |
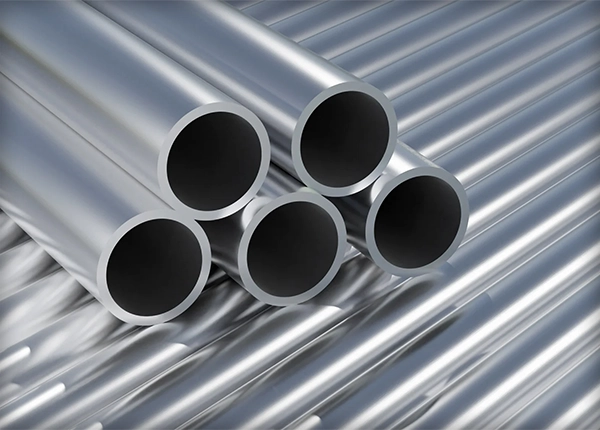
Major Applications
1. Automotive Industry
Engine blocks & cylinder heads (A356, A319)
Pistons (AlSi12CuMgNi)
Wheels & transmission cases (A356, A357)
2. Aerospace & Defense
Lightweight structural components
Heat-resistant housings
3. Industrial & Consumer Goods
Heat exchangers & radiators (4047)
Power tool housings
Cookware & electronic enclosures
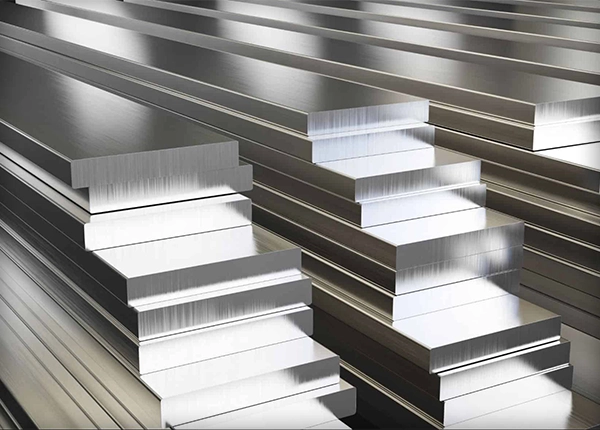
Advantages Over Other Alloys
Better castability than pure aluminum or Al-Cu alloys.
Lower melting point, reducing energy costs in casting.
Good machinability after casting.
Disadvantages & Limitations
Lower ductility compared to wrought aluminum alloys.
Requires modification (e.g., strontium treatment) to refine silicon particles.
Conclusion
Aluminum-silicon alloys are indispensable in industries requiring lightweight, high-strength, and precision-cast components, especially in automotive and aerospace sectors. Their versatility, combined with advancements in heat treatment and alloy modification, ensures their continued dominance in manufacturing.
Add comment