Pure aluminum (often referred to as 1000-series aluminum) is a soft, lightweight, and highly corrosion-resistant metal with excellent electrical and thermal conductivity. Unlike aluminum alloys, which contain added elements like copper, silicon, or magnesium, pure aluminum (typically 99% to 99.9% Al) is used where malleability, corrosion resistance, and conductivity are more critical than strength.
Properties of Pure Aluminum
Property | Value/Description |
---|---|
Purity | 99.0% – 99.9% Al |
Density | 2.7 g/cm³ (Lightweight) |
Melting Point | 660°C (1220°F) |
Corrosion Resistance | Excellent (forms protective oxide layer) |
Electrical Conductivity | ~62% of copper (used in power lines) |
Thermal Conductivity | High (used in heat exchangers) |
Strength | Low (but can be work-hardened) |
Machinability | Poor (soft and sticky, but good for forming) |
Key Advantages:
✔ High corrosion resistance (ideal for chemical & marine applications).
✔ Excellent electrical & thermal conductivity (used in wiring and cooling systems).
✔ Highly ductile & malleable (easy to roll into foil or extrude).
✔ Non-toxic & food-safe (used in packaging and cookware).
Limitations:
❌ Low mechanical strength (not suitable for structural parts without alloying).
❌ Poor wear resistance (soft and prone to scratches).
Common Grades of Pure Aluminum
Grade | Purity | Key Uses |
---|---|---|
1050 | 99.5% Al | Chemical tanks, reflectors, sheet metal |
1060 | 99.6% Al | Electrical components, heat sinks |
1100 | 99.0% Al | Food packaging, heat exchangers |
1350 | 99.5% Al | Electrical wiring (conductors) |
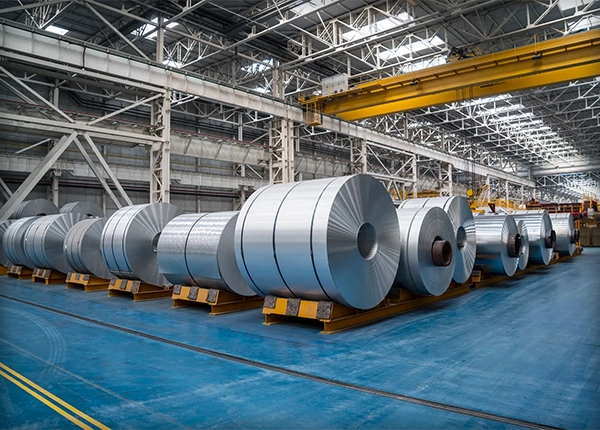
Major Applications of Pure Aluminum
1. Electrical Industry
Power transmission lines (1350 alloy, due to high conductivity).
Busbars, capacitors, and transformers.
LED heat sinks & electronic enclosures (1060, 1100).
2. Packaging & Foil
Aluminum foil (for food, pharmaceuticals, and insulation).
Beverage cans & food containers (1100 alloy).
Flexible packaging (laminated films).
3. Chemical & Marine Applications
Chemical storage tanks (resistant to acids and alkalis).
Piping for corrosive fluids.
Shipbuilding components (due to saltwater resistance).
4. Heat Transfer Systems
Heat exchangers (in HVAC and refrigeration).
Radiators & cooling fins (1060, 1100).
5. Decorative & Architectural Uses
Reflective surfaces (mirrors, light fixtures).
Architectural cladding & roofing (due to corrosion resistance).
6. Food & Pharmaceutical Industry
Cookware & kitchen utensils (non-reactive with food).
Pharmaceutical packaging (blister packs, foil seals).
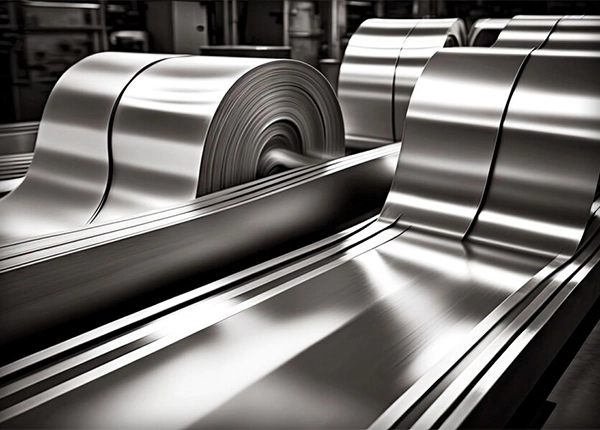
Comparison with Aluminum Alloys
Factor | Pure Aluminum | Aluminum Alloys (e.g., 6061, 2024) |
---|---|---|
Strength | Low (but ductile) | High (alloying improves strength) |
Corrosion Resistance | Excellent | Varies (some alloys need coatings) |
Conductivity | High | Lower (due to alloying elements) |
Machinability | Poor (soft) | Better (some alloys machine well) |
Cost | Lower | Higher (due to alloying process) |
Conclusion
Pure aluminum is essential in industries where conductivity, corrosion resistance, and formability outweigh the need for high strength. From electrical wiring to food packaging and chemical tanks, its versatility ensures widespread use. However, for structural or high-stress applications, aluminum alloys (like 6061 or 7075) are preferred due to their superior strength.
Add comment